Preventative Maintenance Programs for Loading Dock Equipment
Protect Your Investment with Scheduled Dock Equipment Maintenance
At Maxim Services, we understand that functional dock equipment is directly tied to your facility's operational efficiency and overall profitability. Unexpected equipment failures lead to costly downtime, delayed shipments, and potential safety hazards. Our preventative maintenance programs are designed to keep your loading dock equipment operating smoothly year-round.
Benefits of Preventative Maintenance
- Reduced Downtime: Identify and address potential issues before they cause equipment failure
- Extended Equipment Life: Regular maintenance can add years to the lifespan of your dock levelers and doors
- Lower Repair Costs: Prevent major breakdowns that require expensive emergency repairs
- Improved Safety: Ensure all safety features are functioning properly to protect your employees
- Warranty Protection: Many manufacturers require regular maintenance to maintain warranty coverage
- Documented Compliance: Receive detailed maintenance records for safety and insurance requirements
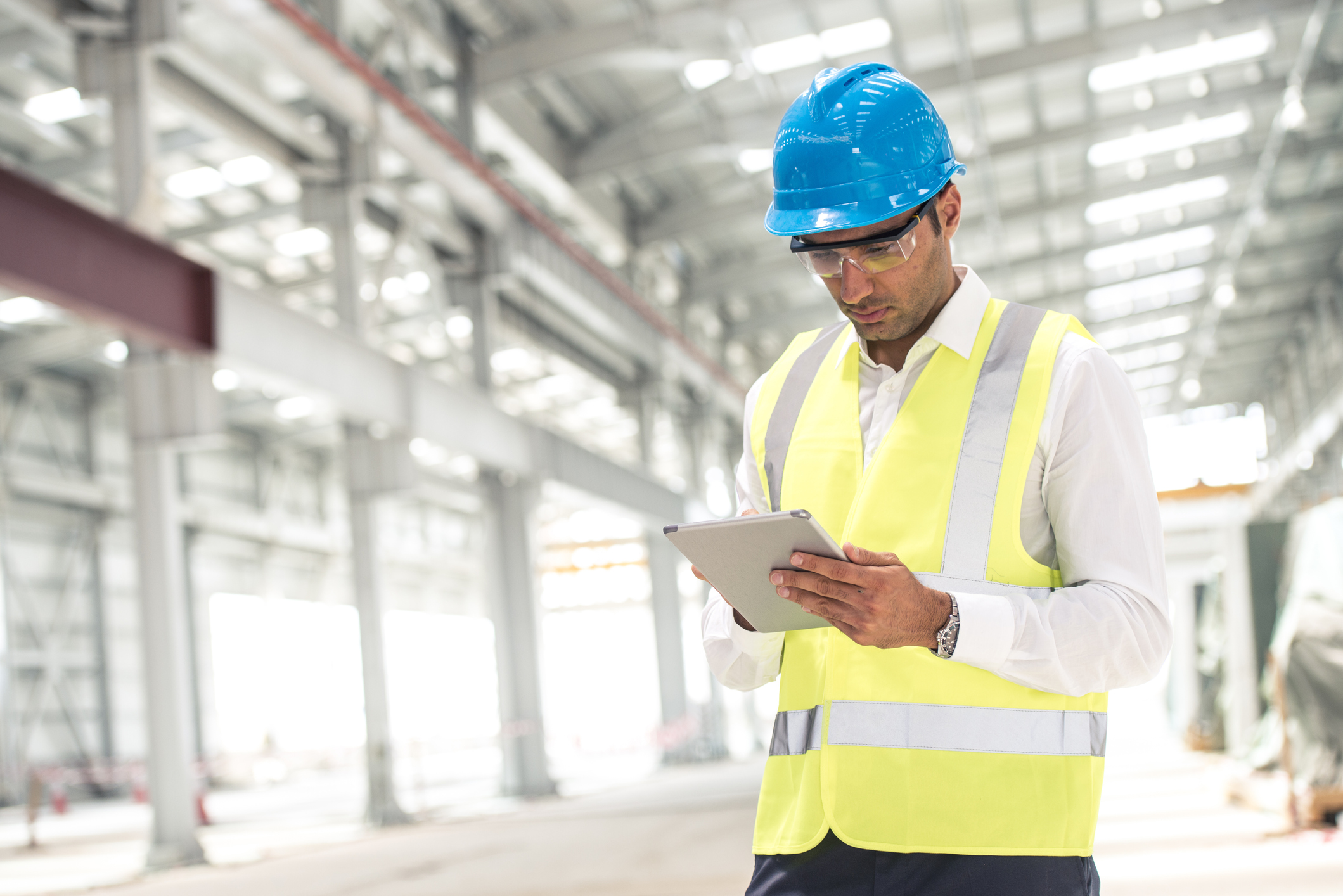
Our Customized Maintenance Programs
Maxim Services has developed customized maintenance programs for all types of loading dock equipment. Our factory-trained technicians follow detailed checklists specific to each equipment type to ensure nothing is overlooked. Our preventative maintenance services include:
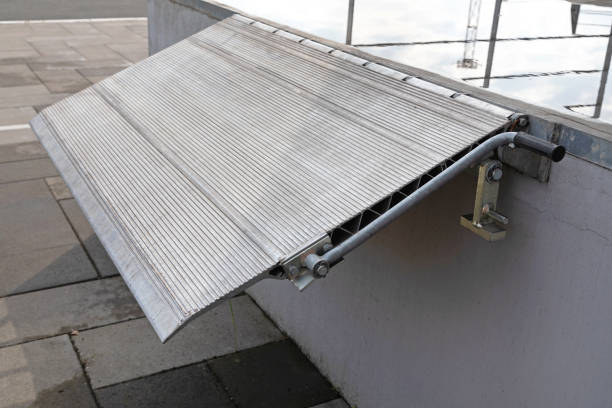
Edge of Dock Levelers & Rolling Sheet Doors
- Complete inspection of all mechanical components
- Lubrication of hinges, rollers, and moving parts
- Adjustment of springs and tension systems
- Inspection and testing of safety mechanisms
- Hardware tightening and replacement as needed
- Operational testing under various load conditions
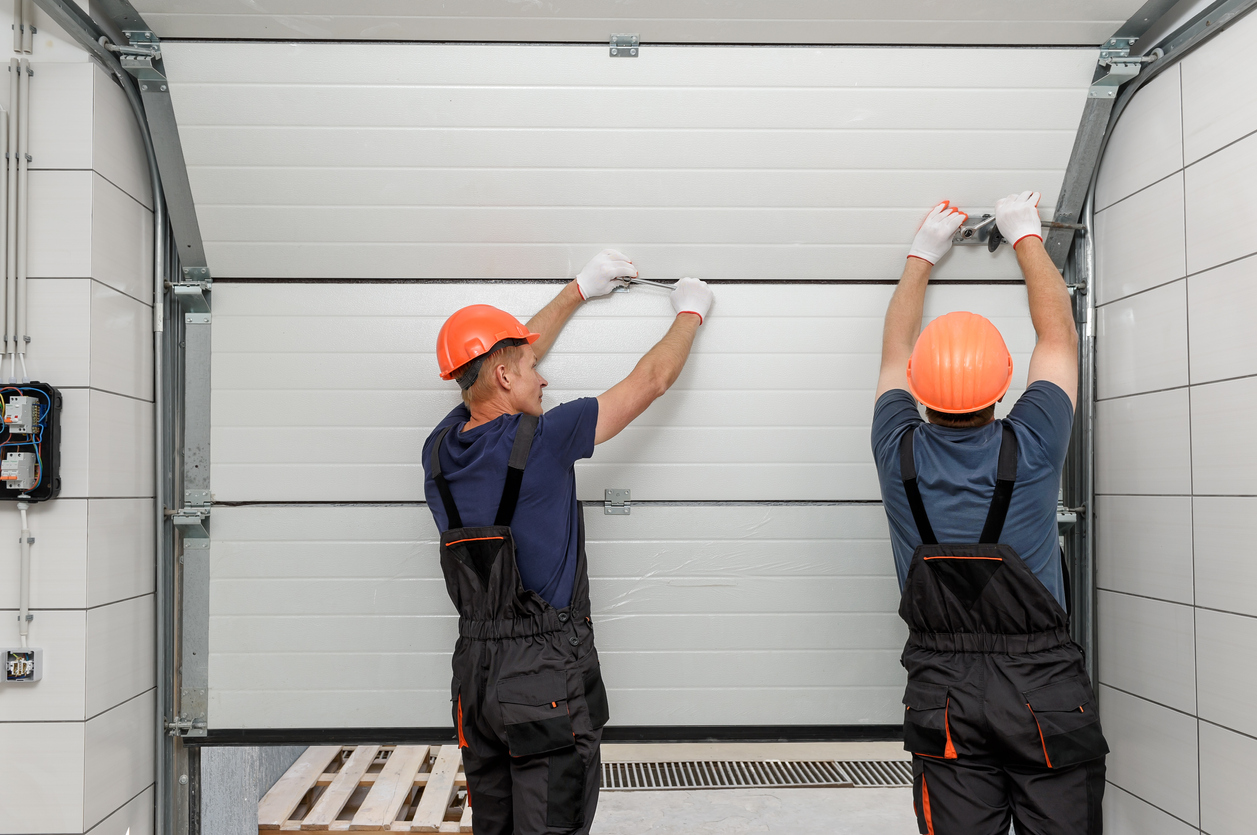
Sectional Overhead Doors
- Comprehensive inspection of door panels, tracks, and hardware
- Lubrication of rollers, hinges, and springs
- Adjustment of tension systems and balancing
- Inspection of weather seals and replacement if worn
- Testing of operational components and safety features
- Cleaning and adjustment of photo eyes and safety sensors
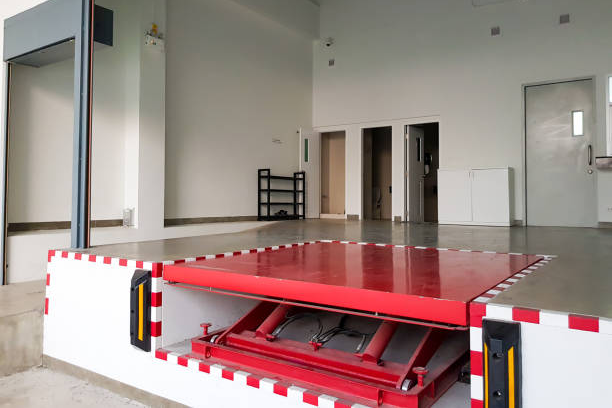
Mechanical & Hydraulic Pit Levelers
- Inspection of all mechanical components and hydraulic systems
- Checking hydraulic fluid levels and condition
- Lubrication of hinges, pins, and moving parts
- Testing of lip extension and retraction Inspection of structural components and welds
- Adjustment of hold-down systems and lip latch
- Verification of proper operation under load conditions
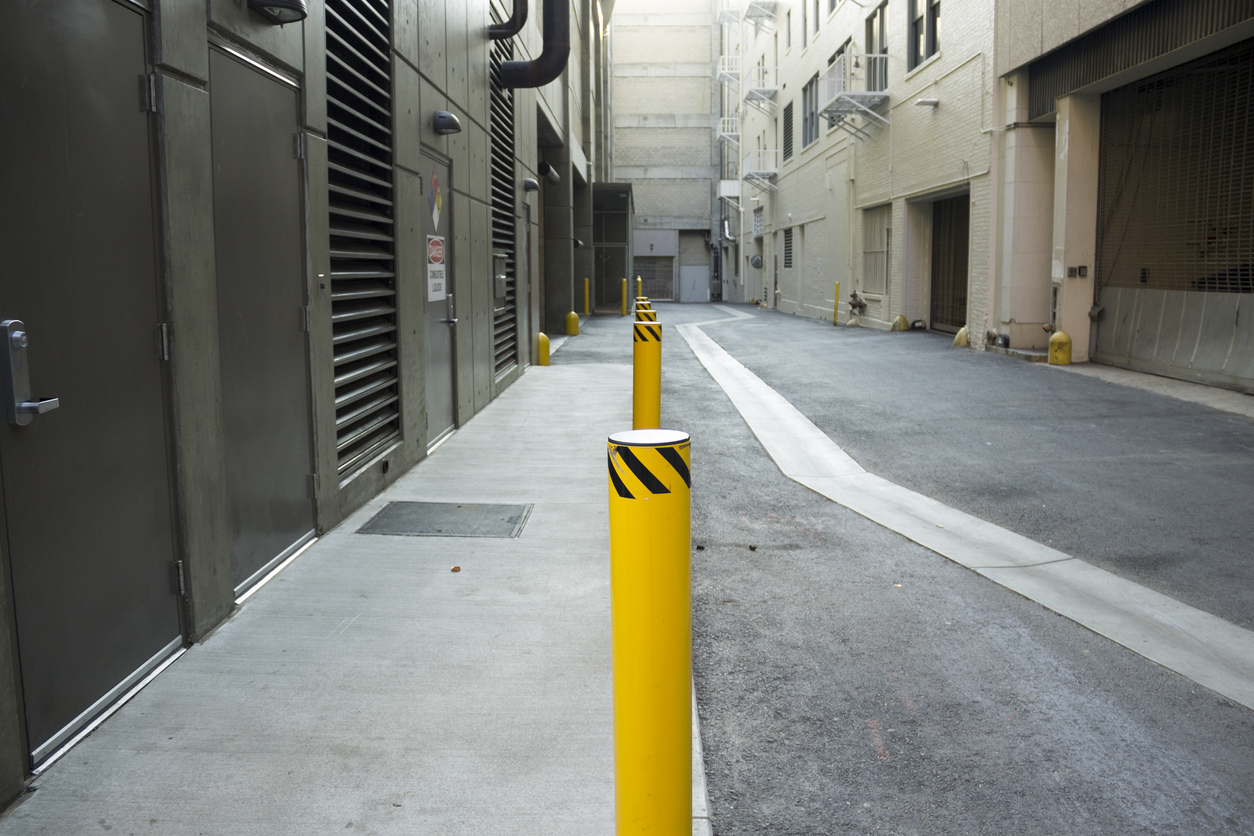
Truck Restraints
- Inspection of carriage assembly and restraining hook
- Lubrication of all moving parts
- Testing of engagement and release functions
- Inspection of communication systems and lights Checking of hydraulic components (for hydraulic models)
- Verification of proper interlock operation with dock levelers
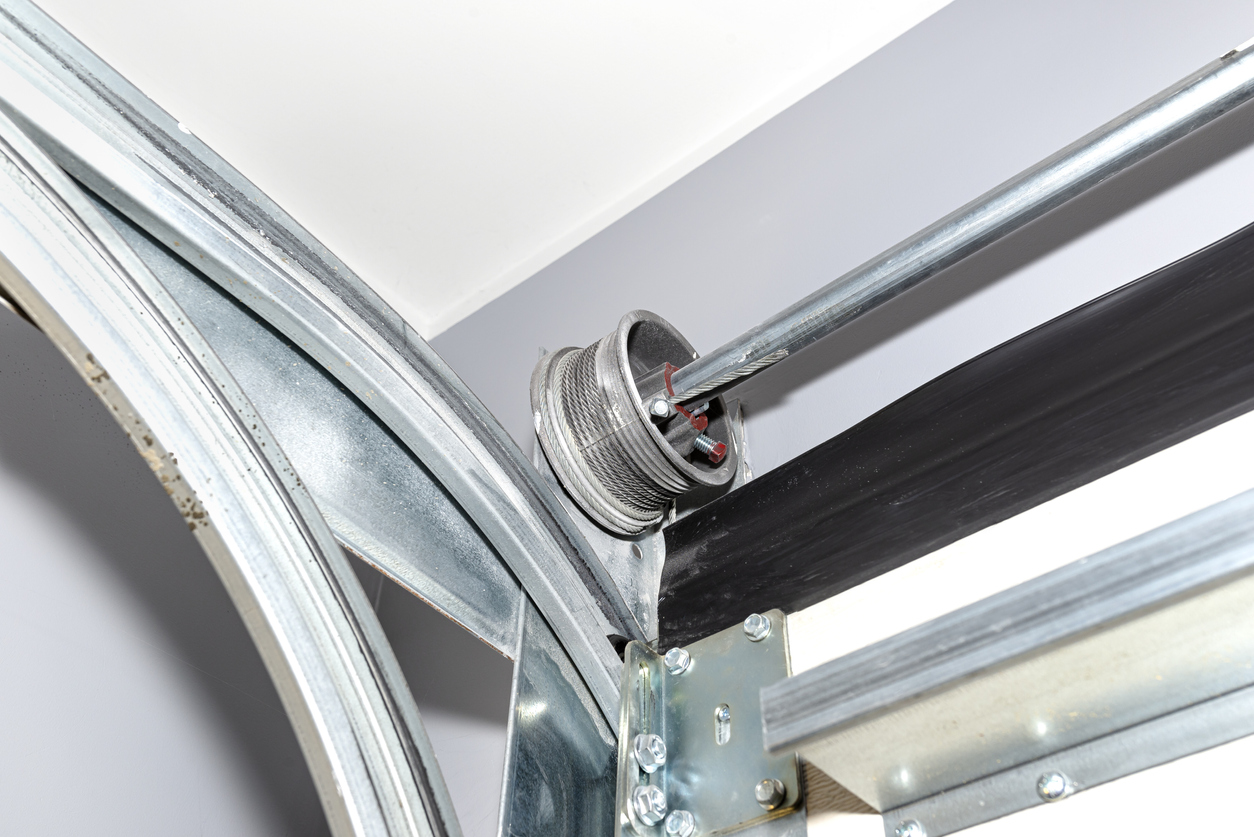
Rolling Steel Service Doors
- Inspection of curtain, bottom bar, and guides
- Lubrication of bearings, guides, and chain drive
- Testing of motor operation and limits
- Adjustment of spring tension
- Inspection of hood and operator mounting
- Verification of safety edge and photo eye operation
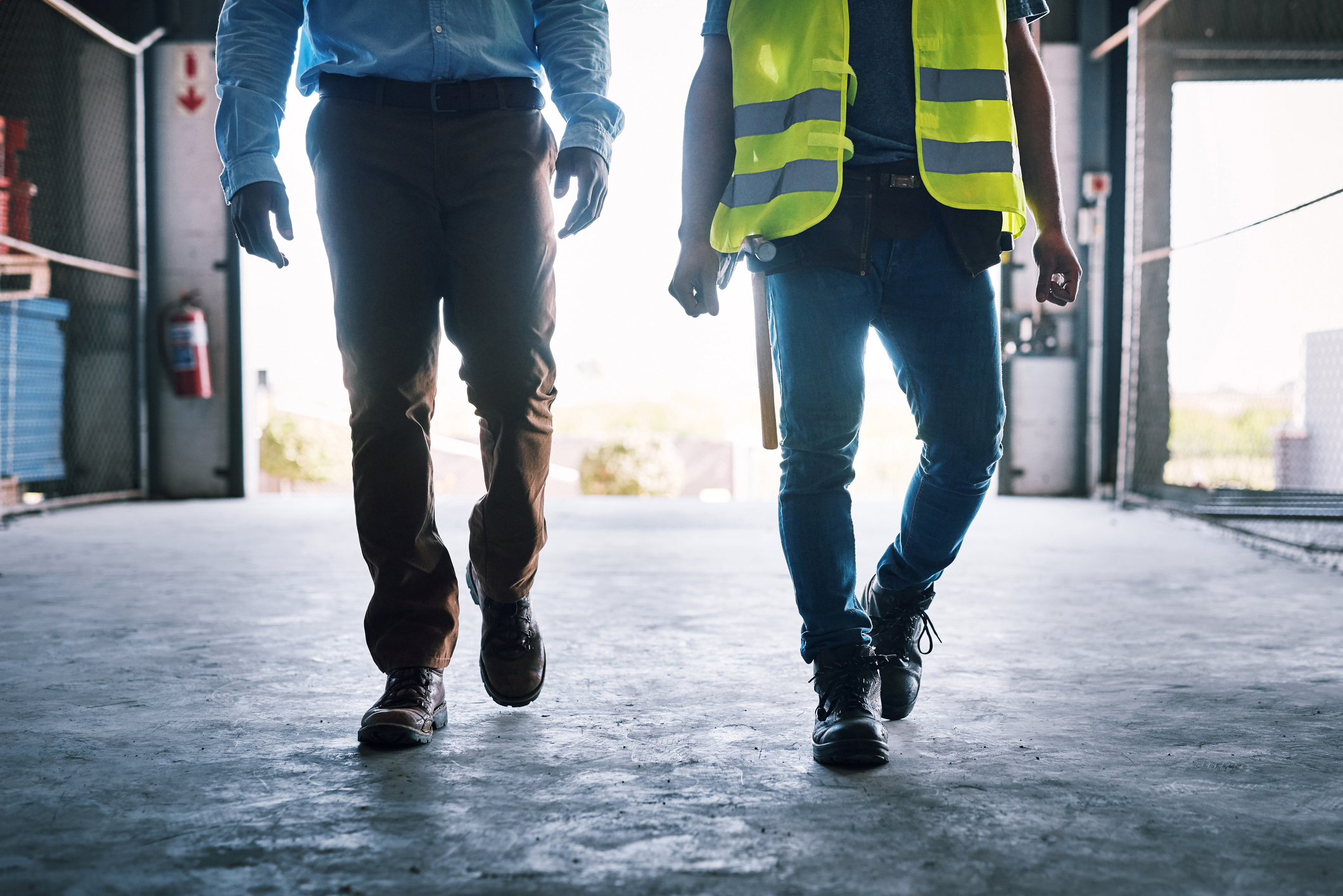
Customized Maintenance Schedules
Based on your facility's specific needs, equipment usage, and industry requirements, we develop customized maintenance schedules:
- Quarterly Programs: Ideal for high-volume operations with multiple shifts
- Semi-Annual Programs: Standard for most commercial and industrial facilities
- Annual Programs: Basic coverage for lower-volume operations
- Custom Schedules: Tailored to your specific operational needs
Emergency Service When You Need It
Even with the best preventative maintenance program, emergencies can occur. As a Maxim Services maintenance customer, you'll receive priority emergency service response when unexpected issues arise.